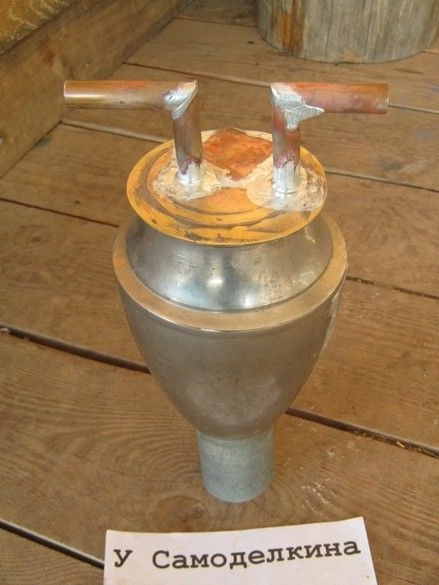
Når de bruges i værkstedet med brandudstyr, fodrer de det i langt de fleste tilfælde med brændbar gas eller en blanding af dem. Hvis du udelader svejsning af metaller, bruges der oftest gas fra byens gasnetværk eller propan. Hvis det er nødvendigt at opnå en højere temperatur, kan der tilsættes ilt til luftblæsningen, eller det erstatter luften fuldstændigt.
Oxygen - gas er meget farlig og ikke for praktisk at bruge. Når det bruges på et værksted, er det nødvendigt at opfylde væsentligt strengere sikkerhedskrav, iltcylindre er designet til et tryk på 150 atm og en standard iltcylinder med en kapacitet på 40 l - den vejer ca. 75 kg, hvilket ikke tillader, at den transporteres og belastes alene. Transport af iltcylindre er underlagt særlige krav.
Der er også en måde, relativt enkel, at øge temperaturen i brænderens flamme lidt - at bruge kulsyreholdig luft (benzin-dampe) til at drive den. En sådan brændbar gas fremstilles i specielle apparater - karburatorer og har adskillige fordele sammenlignet med gas. Dette er naturligvis hovedsageligt den øgede temperatur på brænderens brænder, blandt andet på grund af den ideelle blanding af brændstoffet med oxidationsmidlet. Sammenlignet med gas er benzin sikrere, da dens damp kun forlader tanken, når den renses med luft og får den ind i rummet i farlige mængder, i form af en eksplosion, praktisk taget udelukkes. Forholdsregler for at forhindre gennembrud af flammen inde i slangerne og længere ind i karburatoren er noget enklere end når blanding af ilt i luftsprængningen - flammehæmmere i form af et lille hulrum bag brænderen eller inde i det fyldt med et kobbermudder er ret pålidelige. De behagelige øjeblikke inkluderer placeringen af reguleringsventiler - de er alle (to) placeret på karburatoren og ikke på den varme brænder, hvilket i høj grad forenkler deres liv. Det skal også bemærkes, at tilførslen af flydende brændstof er lettere end gas i cylindre, hvilket er en betydelig fordel i tilfælde af et fjerntliggende værksted.
Dog bruger glasblæsere sjældent benzin som brændstof og foretrækker gas.Disse typer af brændere er populære inden for protetik og smykker og er ret udbredte der. Bruges til lodning og smeltning af en lille mængde metaller - sølv eller guld. Disse brændere er manuelle med forskellige, men relativt lave effekt. Karburatoren er en metalbeholder med loddede dyser. Den ene når bunden og er udstyret med en anden type spray. Luft tilføres den fra en lille kompressor, den bobles gennem et lag benzin, der hældes i tanken og ledes gennem et kort rør til brænderen.
Et diagram af en karburator tilpasset til brug i et glasblæsningsværksted er vist på figuren.
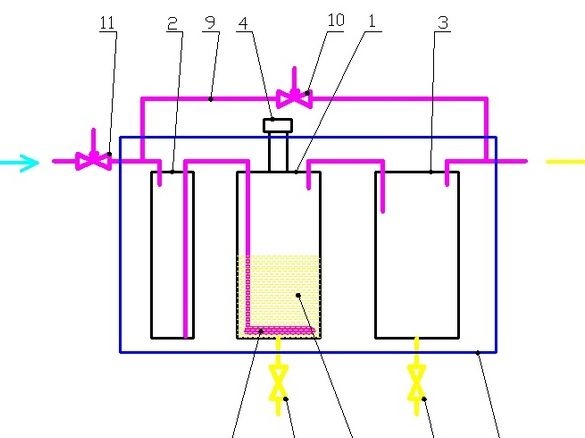
Karburatoren er designet til stationær brug med en glasplader på bordpladen. Enheden har også nogle ekstra bekvemmeligheder - for at øge sikkerheden under brug og har en opvarmningstank med benzin (ikke vist i diagrammet), som giver dig mulighed for at fordampe fra det og forbrænde tungere fraktioner. En forgasser af denne type er beskrevet i [1].
Karburatoren består af tre metalbeholdere 1,2,3. Hovedtanken 1 er en bobler, har en hals med en forseglet hætte 4 på låget, designet til at fylde tanken med gas 5. Et kobberrør loddes ind i bobletanken, når bunden af karet og slutter med en luftforstøver 6. Luft, der passerer gennem mange små huller i forstøveren, bobles gennem benzintykkelsen og mættet med dets par. Et afladningsrør loddes også ind i hætten på bobletanken for at udlede luft med benzin-dampe. I bunden af tanken er der en dræningsventil 7 til dræning af tunge rester af brændstof, vand, eventuelt affald.
Tank 2, fungerer som en fælde i tilfælde af en pludselig afbrydelse i luftforsyningen til hovedtanken og har halvdelen af volumen end halvdelen af tanke 1,2. I dette tilfælde vil benzin på grund af det resterende tryk fra luftblandingen i tank 1 komme ind i tanken 2 og forblive i den. Når lufttilførslen genoptages, vil han skubbe benzin fra tank 2 ind i tank 1.
Buffertanken 3 har de samme dimensioner som tank 1. Den har to forseglede korte rør i låget. En af dem leverer den brændbare blanding fra tanken 1, ifølge den anden går blandingen til brænderen. Tank 3 tjener som en buffer til fældning af dråber, delvis kondensation og opsamling af benzin, hvis dens fordampning i tank 1 er for hurtig. Dette sker, når du udfylder frisk benzin. I den nedre del af tanken er der en dræningsventil 8 til dræning af kondenseret benzin. Denne benzin er af ganske god kvalitet og kan returneres til tank 1.
Mellem karburatorens indløb og udløb loddes et omløbsrør 9 med en nåleventil 10, hvilket tillader en jævn regulering af koncentrationen af brændstofdamp i den brændbare blanding.
Ved karburatorens indløb er der en nåleventil 11 til regulering af luftforsyningen til indretningen.
En elektrisk opvarmning er installeret på hovedtanken 1 for at forbedre benzinets flygtighed, når dens mest flygtige fraktioner føres væk af en luftstrøm. Elektrisk opvarmning er designet til at nå en temperatur på 120 ... 150 ° C og fanger tanken til en højde på 2/3 fra dens bund. Elektrisk opvarmning giver dig mulighed for at bruge brændstof mere dybt og gør systemet mere økonomisk.
Tankene er forbundet med stive kobberrør, anbragt i kasse 12 og fyldt med tørt sand. I dette tilfælde frigøres kranerne 7,8, 10, 11 og benzin 4-halsen udenfor samt dysen til forbindelse til brænderen.
Fyldning med sand ud over at øge enhedens sikkerhed øger dets varmekapacitet og forhindrer pludselige temperaturændringer i enheden (benzin afkøles under fordampning), hvilket fører til udsving i brændstoffordampning og en ustabil fakkel på brænderen. Alt dette gør det mere behageligt at arbejde på en brænder med en sådan karburator.
Så lad os komme ned på fremstillingen. Det er værd at starte med den enkleste del - gasfangskibene.
Til konvertering til karburatorinstallationens fartøjer nærmet man sig to små elektriske samovarer, der lå på loftet. 4l kapacitet TENY, stikventiler, lavet af messing. Til et fældefartøj bad jeg en nabo af samme type om en kedel, uden låg og med en faldet næse - ind garagen han lå rundt.
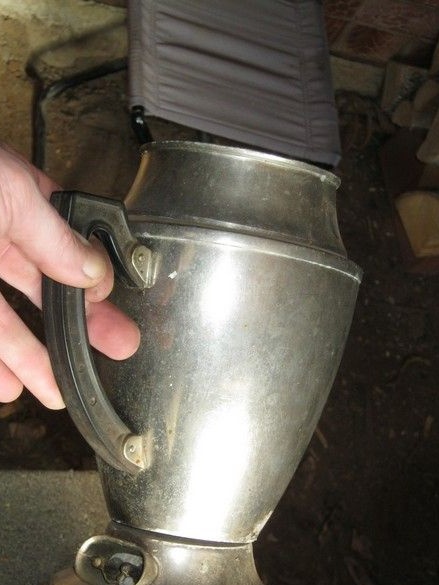
Hvad blev brugt i arbejdet.
Værktøj, udstyr.
Alle forbindelser blev foretaget ved lodning - du har brug for en lille gasbrænder. Sæt med bænkeværktøjer. Slibepude til mellemstor størrelse til slibning af lodningspotter. For en nøjagtig udskæring af kobberrør er det praktisk at bruge en enderpendelsave, eller det vil gøre en miterboks med en båndsav.
Materialer.
Foruden selve kedlen blev kobber- og messingtrimminger, tynd ståltråd til teknologiske fastgørelsesmidler og kobberrør med en diameter på 15 mm anvendt. Tinn-kobber loddemetode 3, flux til det. Brush.
Først og fremmest blev kedlen demonteret - popshik med gennemtrængende fedt og havde ventet, indtil den var lidt forsvundet, skruet håndtaget og varmeapparatet, sidstnævnte brød stadig indeni og måtte tænke.
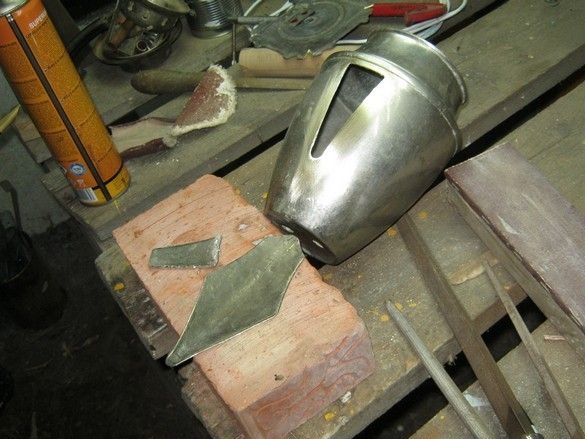
For at forsegle hullet i kroppen fra dysen var dysen i sig selv, udstedt af den tidligere ejer desuden, nyttig. Den blev loddet og udglødet for blødhed, derefter blev den udjævnet på ambolten og renset - det viste sig at være et fremragende stykke ark messing, endda noget større end nødvendigt. Han lagde det på hullet, let bøjet over formen på kroppen, så det passede tæt og skitserede silhuetten af hullet indefra med en filtspids.
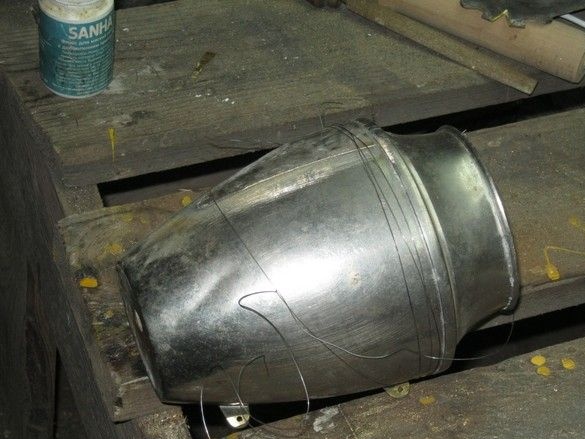
Efter at have skåret med en "grinder" sagede han en smule af og sløvede de skarpe kanter med en fil. Jeg rensede begge overflader før lodning, påførte en loddemiddel og fikserede den med en tynd stålwire. Du kan lodde.
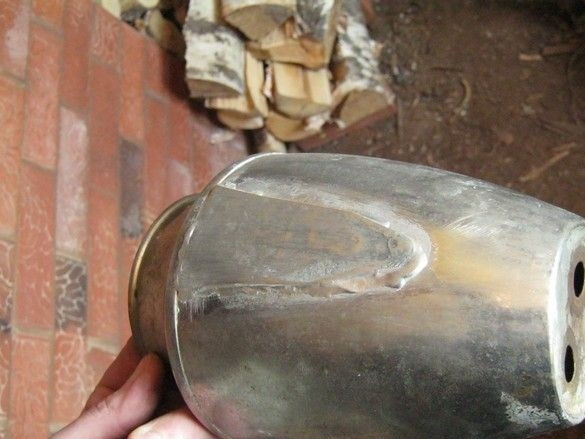
Efter lodning fjernede han ledningen, vaskede resten af fluxen med vand ved hjælp af en pensel.
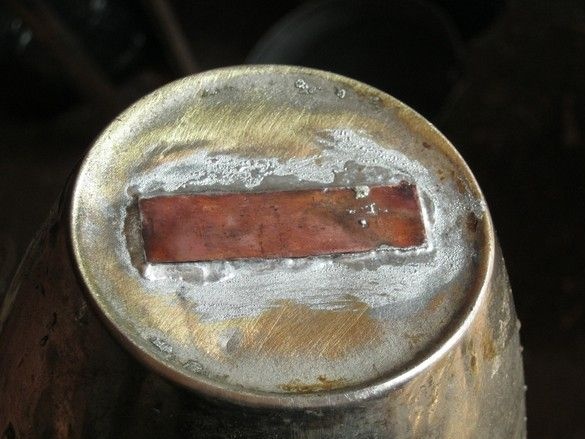
På samme måde forseglede han hullerne fra varmelegemet i bunden. Jeg hentede et stykke kobber med passende tykkelse i resterne.
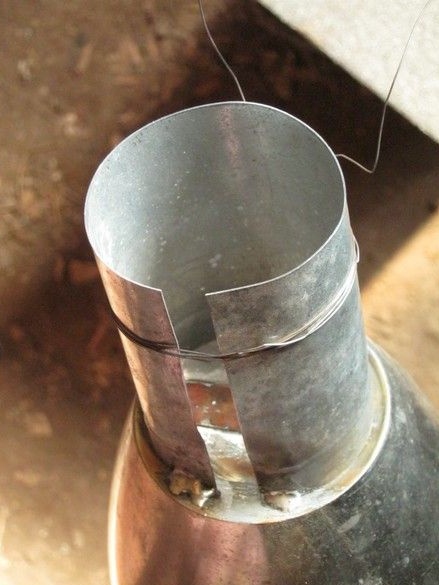
Mine samovarer, hvorfra de resterende dele af karburatoren vil være lavet, lidt højere end vores kedel, og for ikke at lave for lange rør af dyre kobber lavede jeg et lille stativ et glas vulgært galvaniseret, heldigvis er det perfekt loddet med de samme midler. Selve koppen rullede op og bankede med en kamke på en træskive bundet med tråd ovenfra. Jeg trak et emne ud fra den ene kant, så det ikke brændte under lodning, rensede det op, loddet på tre punkter.
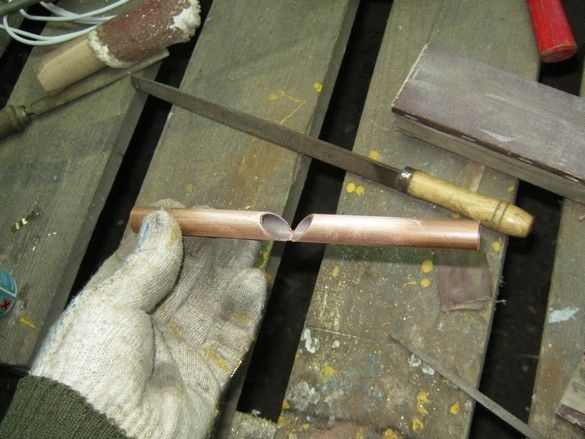
Nu rørene. Rørene, der blev brugt i dette design, er 15 mm kobber fra kobbervandforsyningen. Det ville være mere korrekt at bruge regelmæssige vinkler-koblinger-adaptere, dette ville i høj grad forenkle og styrke designet. Men det hele skadede mig langt fra mig, og der blev truffet en beslutning om at komme forbi, hvad der er - rør med flere diametre og flere typer forbindelsesdele var tilgængelige, hvilket forblev fra et andet design.
Når der endda bøjes et udglødet rør med en sådan diameter, er det vanskeligt at opnå en acceptabel bøjningskvalitet. Det blev besluttet at fremstille en “90 graders” vinkel ved lodning. Enderne af røremnerne blev trimmet ved endesaven. Pænt, med briller og hovedtelefoner, med en lille tonehøjde.
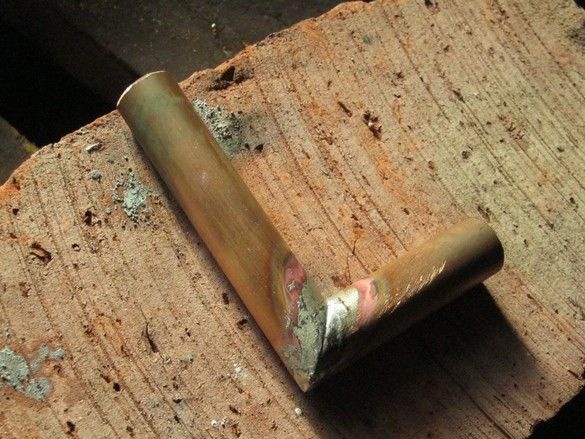
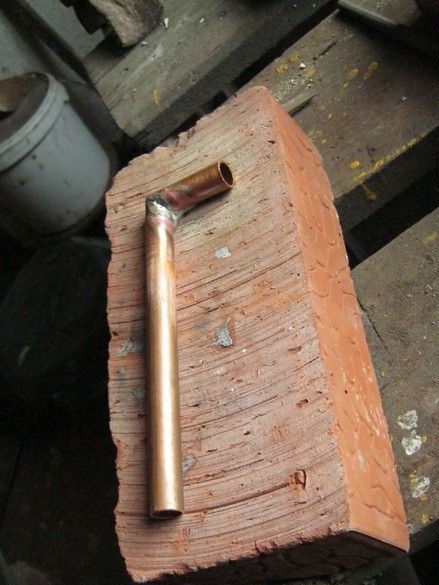
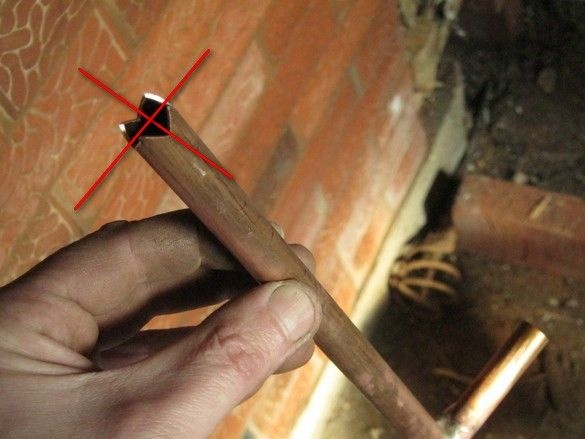
Røret, der når næsten til bunden, bør ikke overlappe hinanden, når man rører ved bunden, men også være meget tæt på det, så den benyttede benzin pumpes tilbage så meget som muligt. For at indstille denne afstand til persiennen lavede jeg sådanne afstandselementer, holdt røret i en skruestik og sagede rillerne med hjørnet af en lille firkantet fil.
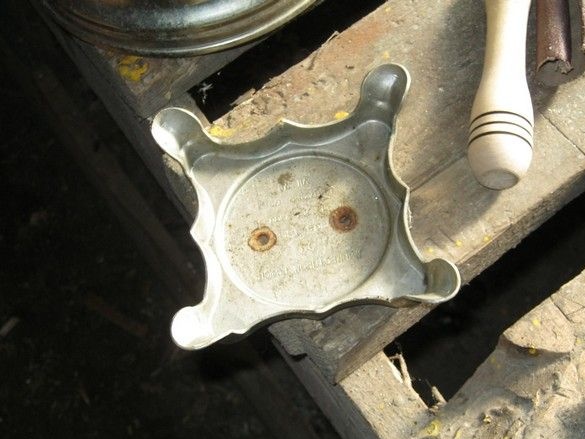
Regelmæssigt var lokket på den tekande, jeg fik, desværre fraværende, jeg måtte opfinde mit eget. Et stort stykke tykt messing var meget ked af det og besluttede at rette stativet ud fra en af samovarer. For at gøre dette anneales det på de brændende kul i ovnen.
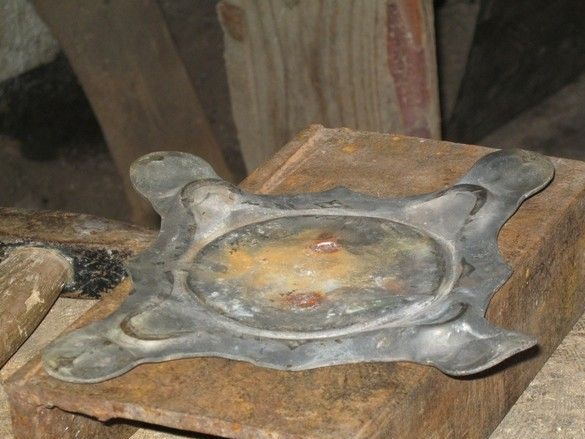
Aften, men ikke helt - stadig glødende.
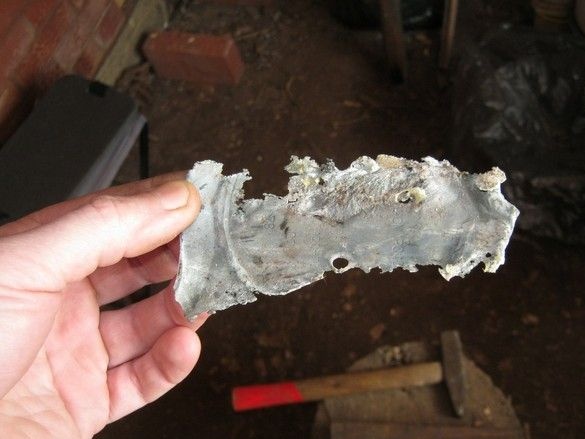
Han besluttede at annealere som det skulle og begravet det i godt brændende kul. Åh du til mig! Alt var væk kok. Jeg var nødt til at bruge leveringen fra den anden samovar og være forsigtig med udglødning.
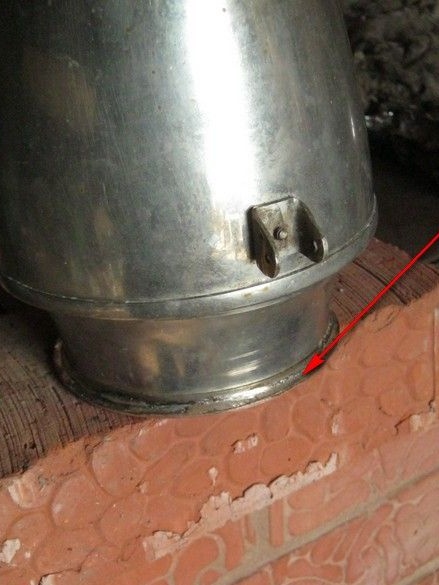
Ved at skære det nødvendige emne ud af den resulterende plade borede han og kede huller til rør med en rund fil. Rengør den grundigt og halsen, forseglet.
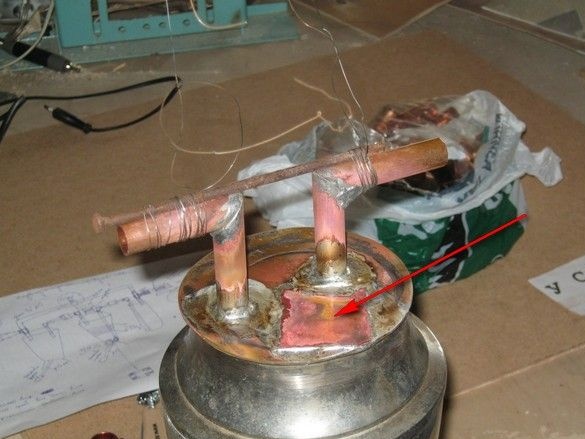
Først loddet jeg et langt rør, derefter med et rør på samme niveau med det, loddet et kort til at fikse rørene under lodning, indpakket en lang søm med wire.Pilen viser plasteret, som stadig skulle sættes i hullet fra den elektriske blok af samovaren.
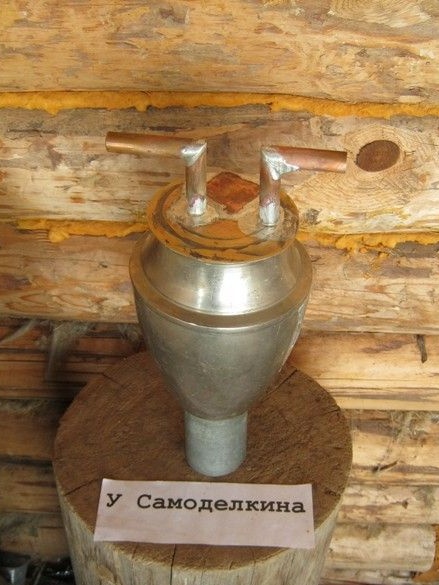
Vasket fluxresterne med vand. Voila!
Del 2. Bubbleren
Litteratur.
1. Veselovsky S.F. Glasblæsningsvirksomhed. 1952.
2. Bondarenko Yu.N. Laboratorieteknologi. Produktion af gasudladning lyskilder
til laboratorieformål og meget mere.