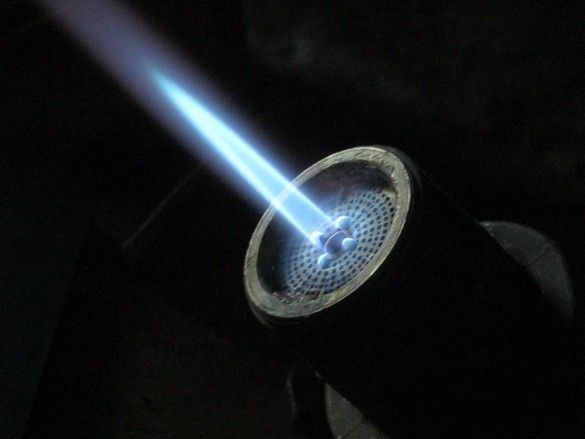
En bordplade-brænder er det største glasblæseværktøj, uanset om det er glasinstrumentfremstilling eller fremstilling af sjove figurer og dekorer. Brænderen danner en flamme, praktisk til blødgøring af glasset og efterfølgende operationer med det. I dette tilfælde bliver det nødvendigt at opnå forskellige temperaturer og former for lommelygten.
Ved en tilfældighed fik jeg en lille glasblæsende lommelygte, der dannede en temmelig tynd ureguleret flammeål. Selv når man arbejder med benzin-dampe (flammetemperaturen er højere end for en gas-luft-flamme), var brænderkraften ikke nok til at arbejde med dog store arbejdsemner. For en vis stigning i varmefluxen blev to brændere samlet - en bærbar gas blev tilføjet i den modsatte retning eller lignende.
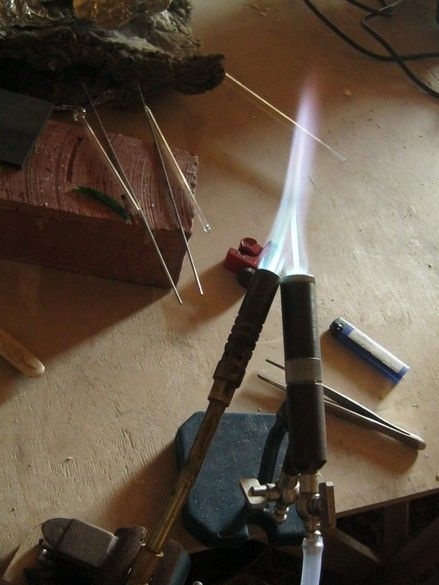
Det viste sig en fluffy flamme, med en højtemperaturnål i midten. Tingene blev sjovere, det blev muligt at oppustes et 10 mm rør. Det næste logiske trin var fremstilling af en mere kraftfuld brænder, der brænder benzindamp.
Det vil være en prototype af brænderen lavet af improviserede materialer - dette er hovedsageligt VVS-komponenter. Dele blev bearbejdet uden en metal drejebænk. Brænderen kører på benzindampe og er baseret på glasblæseren Yuri Nikolayevich Bondarenko [1], en glasblæser-astronom, der fremstiller gasudladningsanordninger. Løsningerne på nogle enheder blev lånt fra dens design, ellers gentager brænderen det design, der er kendt for juvelerer og tandlæger.
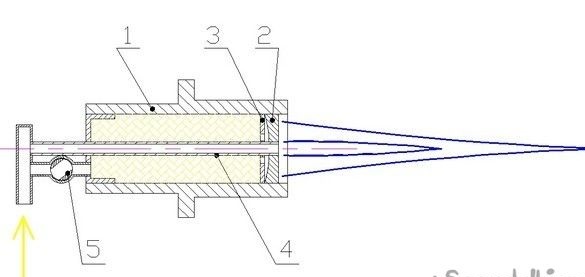
Dens base er et hult cylindrisk legeme 1, koaksialt, som dysen 4 passerer igennem. Korkhanen 5 giver dig mulighed for at justere formen på faklen - når du åbner den, kommer en del af den brændbare blanding ind i kroppen ud over dysen og formes til brænderen med gitter 2. Åbning 3, kombineret med formen på gitteret 2 og det resulterende linseformede hulrum koncentrerer strømmen af den brændbare blanding hovedsageligt langs brænderens akse. Disse dele er lånt fra mentorens brænder [1]. På dyserøret er der flere huller, der leverer lidt gas til gitteret (ikke vist på skitsen) og med en helt lukket vandhane 5 til dannelse af en lille bærende fakkel.Det tillader ikke at hovedbrænderen går i stykker - "nålen" ved høje gasstrømningshastigheder. Disse huller vælges, når brænderen sættes op.
Værktøj, udstyr.
En blødgaslodder har brug for en lille gasbrænder. Sæt med bænkeværktøjer. Elektrisk slibeapparat. Der blev brugt en drejebænk og en boremaskine. Vise.
Materialer.
Foruden jernstykkerne var der behov for et kobberrør med en diameter på 6 mm. Tinn-kobber loddemetode 3, flux til det. Korkhane fra en samovar.
Emnet til brænderlegemet var en fabriks bronzetilpasning fra en VVS-butik med en indvendig diameter på 30 mm. Der blev også købt flere forskellige dele der, hvoraf nogle også senere blev brugt som emner til brænderelementer.

Et af beslagene bruges som hus uden ændringer. Armaturet blev ikke tændt på ydersiden - den store vægtykkelse og tidevand giver kroppen en yderligere varmeafledning.
Størrelsen på VVS-propperne blev valgt, således at den resulterende del med minimal drejning af gevindet passede ind i den indvendige kanal i fittingen. Jeg sliber træ på en drejebænk, for dette vendte jeg en simpel snap, som jeg plantede et emne på.
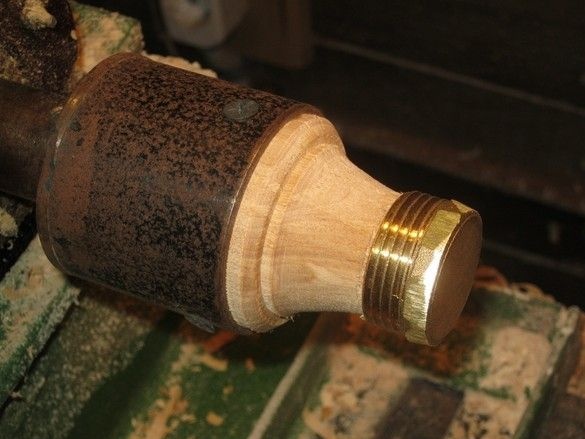
Landingstæthed tilladt mere, ingen måde at fikse delen på. Stærkt indtastede hjørner af en nøglefærdig sekskant er tidligere jordet på en slibemaskine. Omsætning - ca. 1000 o / min, første grov drejning med en lille "slibemaskine" - delen roterer, slibemaskinen fungerer. Efter færdigbehandling af filen blev den midterste hud fastgjort på en træblok. Den endelige fastgørelse af emnet gjorde det muligt nemt og ofte at prøve det til “arbejdsstedet” - den resulterende del kommer tæt ind i huset med ringe anstrengelse.
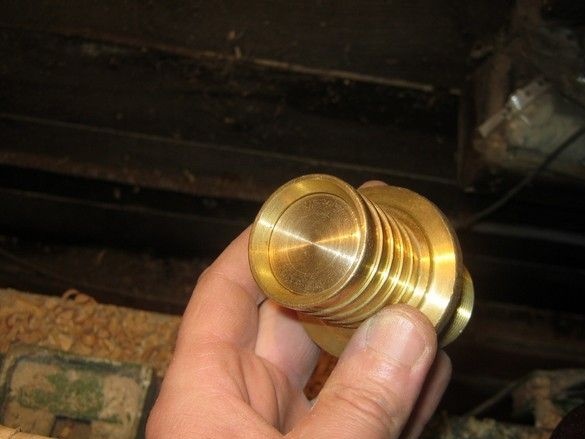
Vi går videre til den komplekse og afgørende detalje - gitteret. For det første et par teoretiske overvejelser.
Gitteret, ud over at distribuere den brændbare gasblanding, er også ansvarligt for sikkerheden - de vil ikke tillade, at flammen trænger ind indenfor og undgår en ”modstød”. Dette er sandt, da vores brændstofblanding tilberedes i ballon "pære" og ikke som sædvanligt - i stedet for brænderen. I denne type brænder til fuldt arbejde med glas, inklusive ildfast glas, såsom Pyrex, er det nødvendigt at tilføje eksplosiv gas fra elektrolysatoren.
Flammen, der passerer indeni, gennem gitteret, afkøles så meget, at den går ud. Der er et koncept - det ultimative hul. Dette er den maksimale diameter på de "dybe" huller, der kan udføre en flammehæmmerfunktion, og den er forskellig for forskellige gasser. For eksempel for benzindampe i luften, hvis flammeudbredelseshastighed er lille, det begrænsende hul er ~ 0,9 ... 1 mm, men så snart ilt eller eksplosiv gas trænger ind i systemet, hvilket væsentligt øger flammeudbredelseshastigheden, skal hullerne i det beskyttende "mesh" laves væsentligt mindre. Den maksimale diameter på huller, for eksempel for ren eksplosiv gas, ~ 0,3 mm, hvilket repræsenterer en vis vanskelighed ved fremstilling og drift.
Som et slags kompromis foreslår Yuri Nikolayevich at bruge huller i 0,8 mm gitteret, mens den nødvendige sikkerhedsforanstaltning på værkstedet vil være et ret robust design af "pæren" og "skylning" af elektrolysatoren [1], så de kan overleve en mulig sprængning uden skade. Benzin-karburatoren er lavet af en propancylinder, der vasker elektrolysatoren fra kuldioxid-ildslukkere. Under normal drift af udstyret forekommer der ingen gennembrud. I tilfælde af overtrædelse af normale driftsbetingelser opstår der et klap, der ikke fører til en ulykke.
Meshullernes "længde" giver dens tykkelse. I betragtning af den linseformede form skal maskenes tykkelse være 3 ... 4 mm i den tynde del og 6 ... 7mm i kanterne. Der var ingen færdig plade med sådan tykkelse, jeg var nødt til at kigge efter en donor. Det viste sig at være en temmelig massiv, forældet vandhane til badeværelset. Et relativt jævnt stykke af væggen blev skåret derfra, hvorfra det var muligt at skære et emne til gitteret.
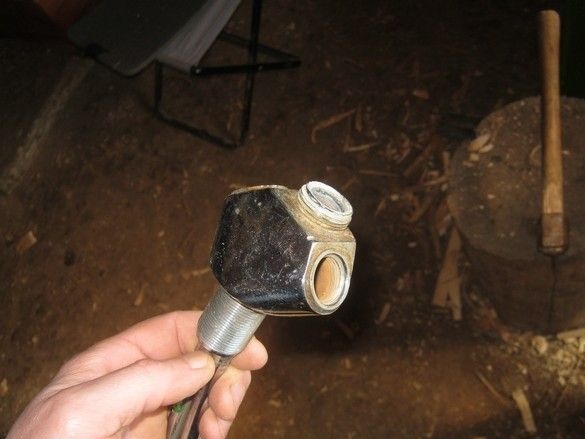
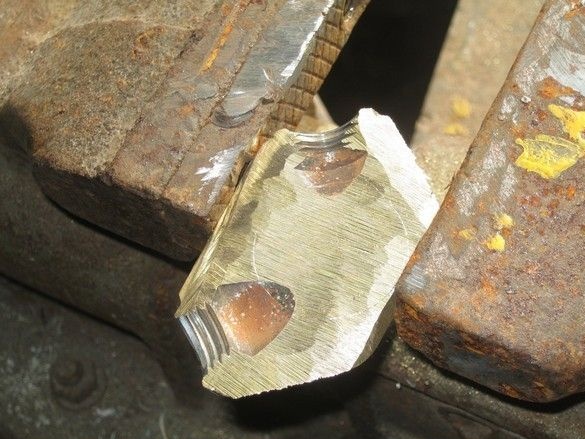
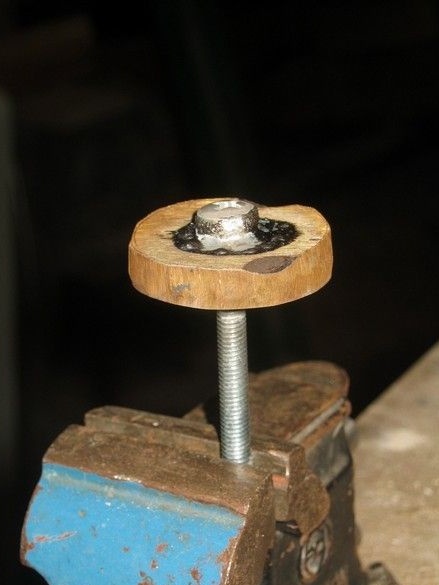
Arbejdsemnet blev, efter grov drejning, monteret (loddet) på M5-skruen, for hvilket emnet kunne fastgøres i en tre-kæbe chuck til justering af størrelse og form.
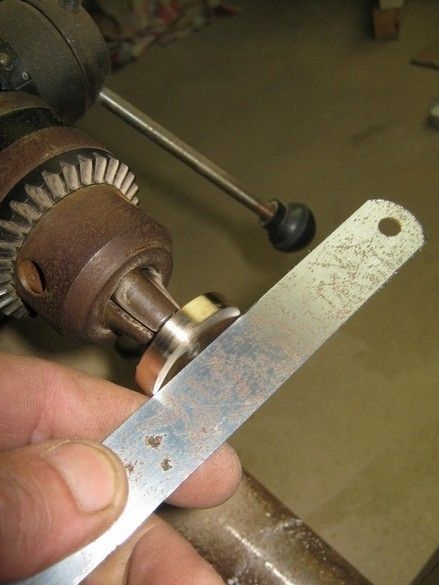
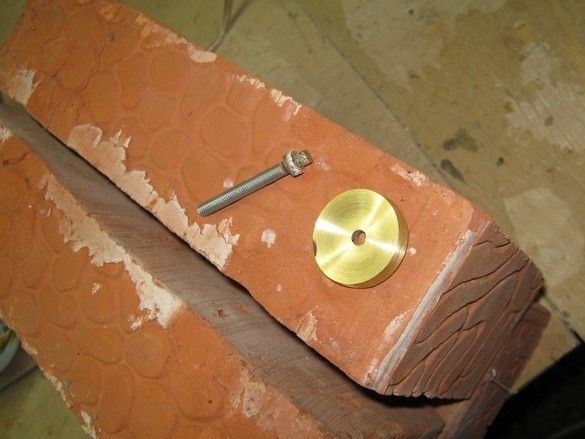
Boremaskine, for at lette betjeningen, blev lagt på dens side. Den konkave overflade i emnet blev bearbejdet nogenlunde - med en lille "slibemaskine", en "rest" af disken (mindre radius), derefter medbragt med et slibesand. Skruen er loddet, så det fremspringende hoved blev slibet sammen med emnet. Efterfølgende blev emnets udvendige diameter bragt til det ønskede. Efter at have drejet, smeltede jeg skaftet fra emnet - resten af M5-skruen. Det resterende hul blev boret til den ønskede 6 mm.
Den næste ansvarlige og temmelig kedelige fase er at vippe midten af fremtidige huller og bore dem. Med det rigtige antal huller og deres diameter er opgaven ikke let. Amatørradiooplevelsen hjalp meget - at stanse og bore et stort antal huller på arbejdsemnerne på trykte kredsløbskort, før opfindelsen af blyfrie (SMD) komponenter, var almindelig praksis.
Hullens diameter er allerede blevet diskuteret, det skal siges om deres antal - deres samlede areal skal være mindst 20% af gitterområdet.
Det er praktisk at tegne huller i AutoCAD, dette program giver dig mulighed for at udskrive en skitse nøjagtigt i en 1: 1 skala. Efter udskrivning blev den resulterende skabelon limet på en flad overflade af gitteret med limblyant, med fokus på det centrale hul, det er praktisk at gøre dette i lyset.
Til skruing brugte jeg en speciel miniatyrkerne. Du skal passe på et godt skarpt lys, et specielt visir med forstørrelsesglass er praktisk til dette arbejde. Arbejdet går ikke hurtigt, og det er vigtigt at organisere et behageligt sted - lidt fri overflade, "operatøren" i siddende stilling. Jeg anbefaler at udføre sådanne operationer i mere end én tilgang. Efter stansning skrælles skabelonen af, resterne vaskes af med varmt vand.
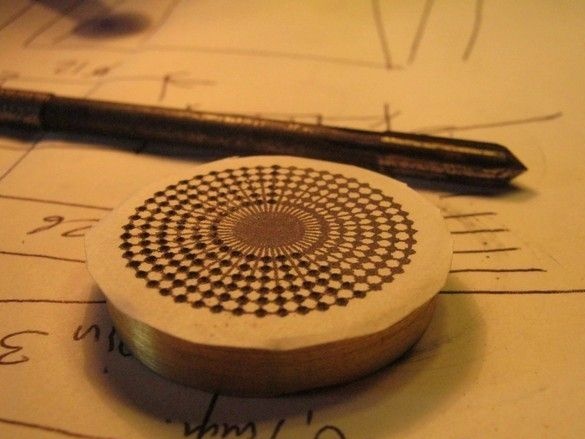
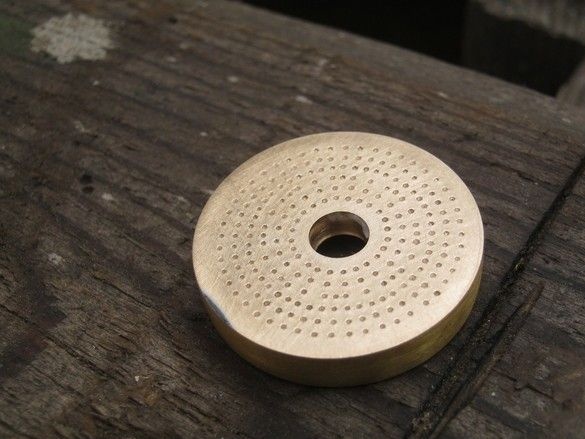
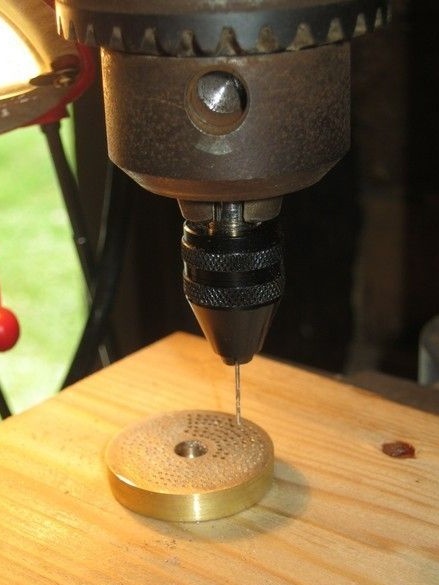
Til boring af denne art - tykt metal, tynde bor, den nødvendige nøjagtighed, er en række håndholdte enheder helt anvendelige. Du skal bruge noget mere stationært. I dette tilfælde blev en miniatyrchuck brugt til at spænde min 0,8 mm boremaskine; chuckskaftet blev klemt fast i en stor tre-kæbe chuck på en bænkboremaskine. Denne kombination gjorde det muligt for os selv at bore med en tynd bore; jeg brød kun en, og selv da helt til sidst.
Det viste sig at være billige øvelser, der blev købt i en radiobutik, og de var af dårlig kvalitet, en slags forenkling fra ideen om en bore. Rillerne til spånafladning på dem var meget lavt. Der er en mistanke om, at de er lavet specifikt til at bore foliefiberglas, og det er bedre at bruge normale "maskinbygning" -bor.
Yuri Nikolayevich siger, at der er tilfælde af bor, der fastklæber under dyb boring, så du skal købe dem med en margen og derefter vælge ikke kiler. Der er en antagelse om, at dette skyldes deres tilspidsning. Boring er noget lettere, når man smører boret med olie eller alkohol, men der skal konstant tilsættes alkohol.
Korrekt slibning af en sådan miniatyrbor er ikke en let opgave, og i mangel af dygtighed er det bedre at bruge nye bor, ellers er en betydelig "træk" uundgåelig, når man borer. Men med omhyggelig boring i maskinen kan alle de nødvendige huller bores med en bor fra en slibning.
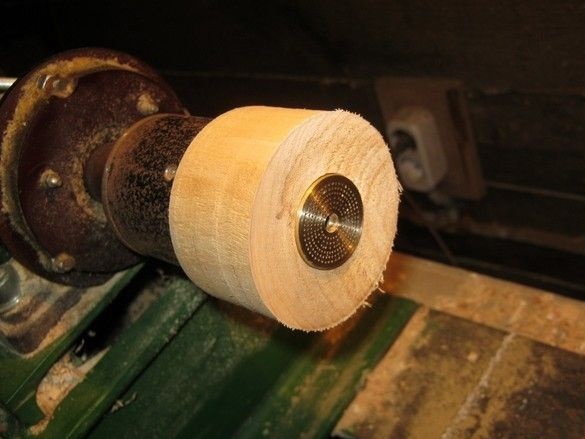
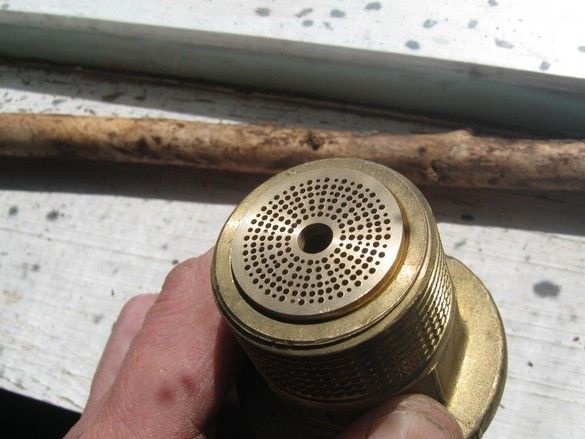
Efter boring skal alle resulterende små burr slibes. Dette gøres mest bekvemt på en roterende del. For at installere gitteret i en drejebænk blev det enkleste udstyr bearbejdet. Meshet passer tæt ind i udsparingen.
Ved fremstillingen af prototypebrænderen skulle det kun arbejde på benzin-dampe, så nogle af hullerne blev forstørret - 1 mm.
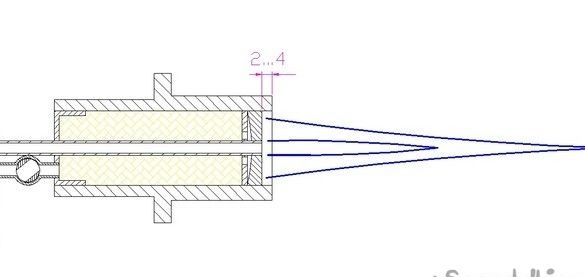
Gitteret er forsænket ind i kroppen med 2 ... 4 mm. Yuri Nikolaevich, anbefaler, at denne størrelse vælges omhyggeligt - hvis der er et overskud, vil brænderlegemet opvarmes meget, hvis det er utilstrækkeligt, er faklen i nogle tilstande tilbøjelig til at gå i stykker.
I min "lavtemperatur" sag - når jeg kun fodrer med benzindampe, uden eksplosiv gas og med en meget massiv kasse, satte jeg den maksimale dybde uden indstilling. Efter det ville det være rart at lodde masken. Dette skal gøres med "hårdt" lodde. Kobber-fosfor er velegnet, men i dette tilfælde er sølvlodde som PSR-45 bedre, det brænder mindre ud. Jeg kunne ikke lodde masken fuldstændigt ind i min enorme kasse, jeg kunne ikke lodde den med lodde - der var ikke nok temperatur, selv når jeg varmet det med en reflektor, en stor blæser. Gitteret kom dog ind i kroppen med en god pasform, så jeg forlod det som det er.
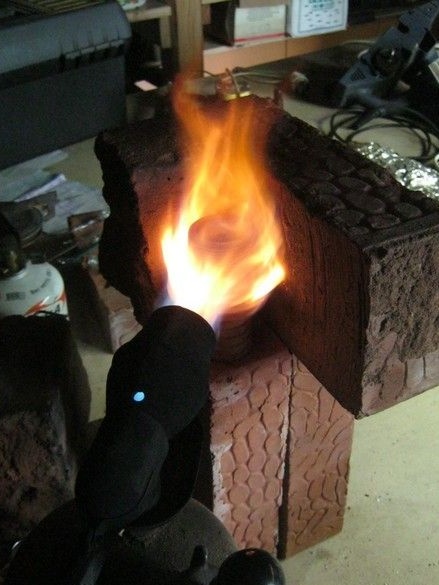
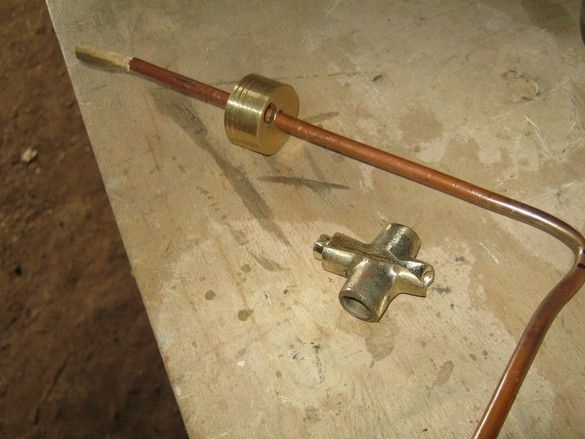
Dyse - en komplet forenkling. Fremstillet i kobberrør med en indvendig diameter på 4 mm. Brug kun som en prøveindstilling. Jeg vil citere fra [1] - ”Dysen skal give en smal laminær strømning af den brændbare blanding og en skarp fakkel i det mindste med en lav flamme. Dets laminaritet kan sikres med en huldiameter på op til 2,5 mm, en længde på mere end 35 mm, en poleret indre overflade og en stabil strømning ved indløbet. Den laminære flamme giver mindre støj og giver dig mulighed for at reducere opvarmningszonen, så du skal prøve at få en laminær fakkel. (Professionelle glasblæsere kan have forskellige meninger om dette emne). Dyseåbningen er bedst lavet konisk - dette giver mindre modstand mod strømning. Endedelen med en længde på cirka ti millimeter skal laves cylindrisk. "
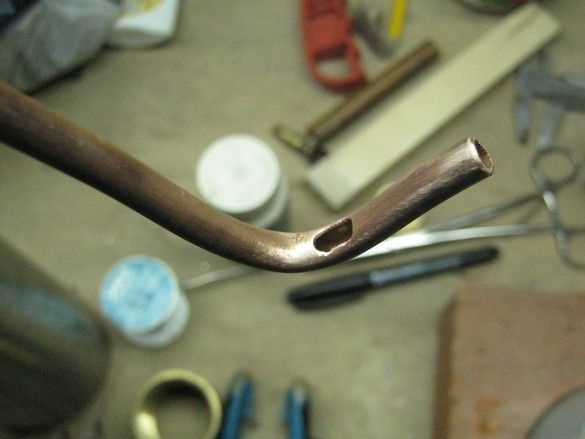
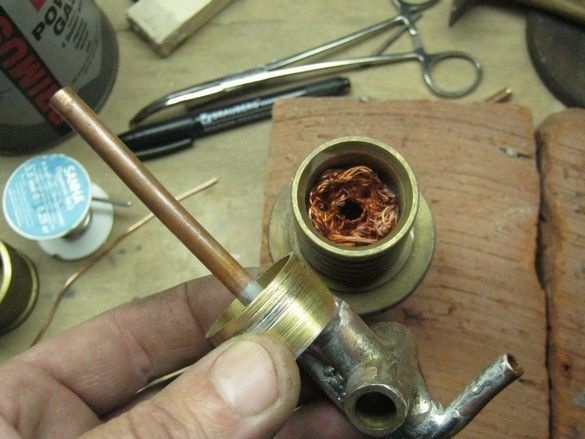
Før bøjning blev dyserøret udglødet og fyldt med tørt sand. Brænderens indre hulrum blev løst fyldt uden særlig fanatisme med et kobbermudder - dette er yderligere beskyttelse mod "gennembrud" af flammen og beroliger gasstrømmen. Polstringen holder også membranen presset fra indersiden til gitteret.
Al lodning "bagved" er fremstillet af tin-kobber loddemetode med et smeltepunkt på ca. 200 ° C. Brænderlegemet opvarmes markant, haledelen er ikke højere end 60 ° C - du kan nemt gribe den i hånden, og selv efter langvarig brug kollapser enheden ikke.
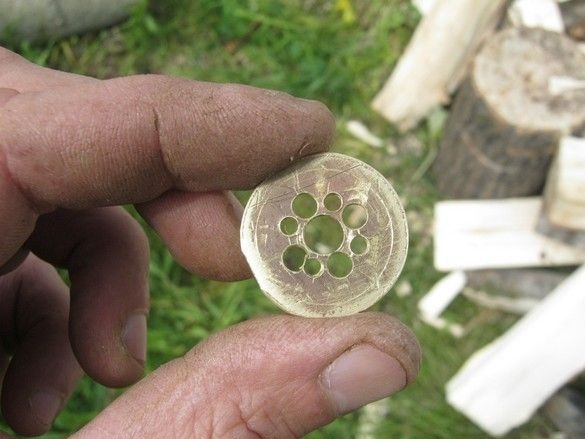
Membranen i sig selv er lavet af en flad 3 mm messingplade. For en mere markant virkning skal "linsen" laves biconvex, for hvilken membranen også skal være konkave. For at gøre dette kan det bøjes ved hjælp af Punzel og Anki, eller slib fra et tykkere emne, der ligner et gitter.
Efter prøveantændelser så det ud til, at faklen var kort, som en sandsynlig årsag, så tynde sektioner af rør, der leverede gas til huset. Brænderen er blevet moderniseret - korkhanekanaler bores til en diameter på 7 mm, det fælles forsyningsrør er udskiftet.
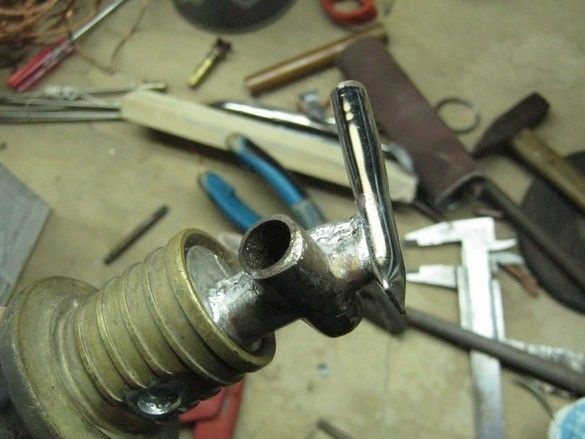
Det blev lidt bedre. Samtidig satte jeg op en bærende lommelygte. Yuri Nikolayevich rådgiver om at arkivere en trekantet fil med riller, en slags stjerne på fem til syv stråler, i hullet i det maske, gennem hvilket den centrale dyse passerer, så der er en forbedret blanding strømme rundt dysen. Det øger stabiliteten af "nålen" og reducerer båsen i turbulent tilstand.
Mængden af brændbar blanding til understøtningsflammen indstilles af huller på dysen inde i huset. Deres antal og størrelse kan tilpasses.
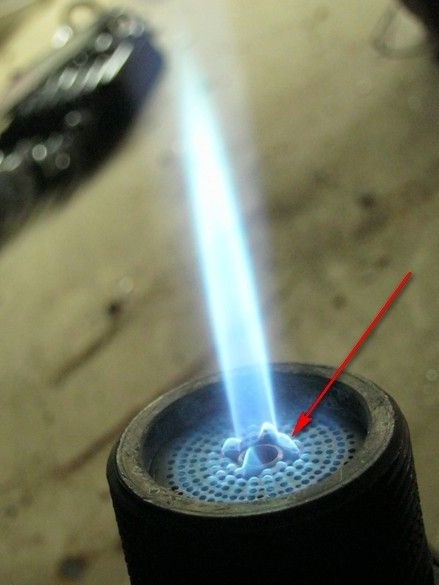
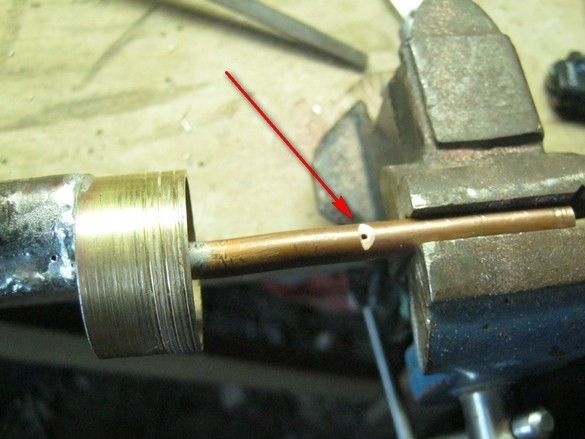
Et par fotos af lommelygten, der hidtil er opnået med forskellige placeringer af vandhanen på brænderen - så at sige, "nål", "blød" flamme og noget derimellem.
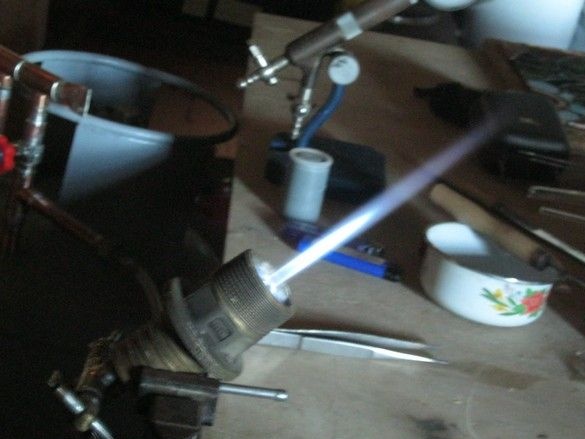
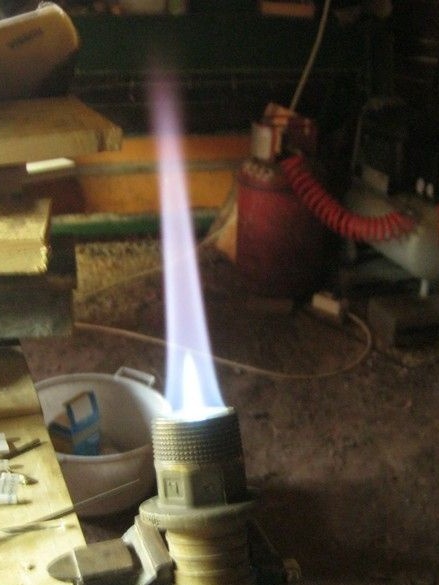
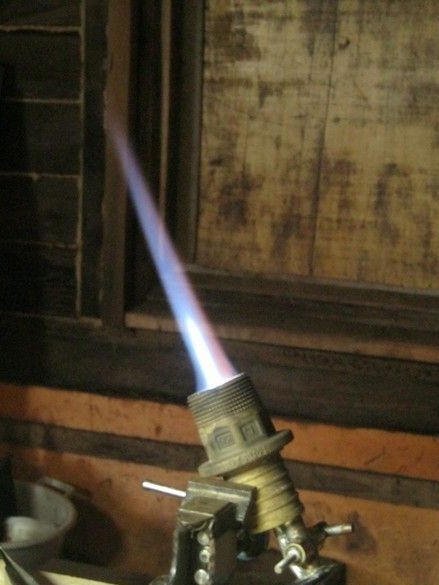
Et "ben" til den eksperimentelle brænder blev ikke lavet; under operation klamrede den sin kasse i en lille bordskrue.
Den resulterende fakkel er meget større end den første lille brænder, selv med tilsætning af en gassøster. Glas varmes meget hurtigere op, og et større område, "flyder", det var muligt at oppustes et 18 mm rør fra smelteligt "neon" glas. Det viser sig, at operationer ikke lykkedes tidligere - drejning af kanterne, gennemboring af et tykt lag glas med en wolframnål.Samtidig mærkes behovet for yderligere at hæve brænderens temperatur. Der er ikke mange muligheder - tilsætning af ilt eller eksplosiv gas.
Arbejd med fejlene. Måder til yderligere forbedring.
Ikke desto mindre bør denne type arbejde udføres ved hjælp af en metal drejebænk, dele og hele strukturen vil være mere nøjagtige og præcise, hvilket gør dem mindre smertefulde. Husets og dysens diameter er åbenlyst for stor, det ser ud til, at det er det, der ikke tillader at få en længere lommelygte af blød flamme - gashastigheden, når den falder ned i et bredt hus (dysen) falder markant. Det er værd at nærme sig størrelsen på brænderen i [1]. Det ville være dejligt at fremstille et dyse, et krop, et net og en membran fra et messingemne og ikke fra noget - designet kan gøres mere praktisk ved montering og justering. Det ville være dejligt at lave en dyse i henhold til chartret - et mejslet, konisk poleret hul (se ovenfor eller [1]). Om ilt eller "klapperslange", er allerede sagt.
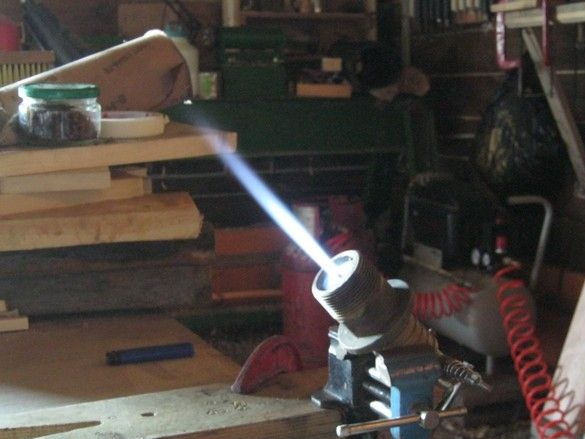
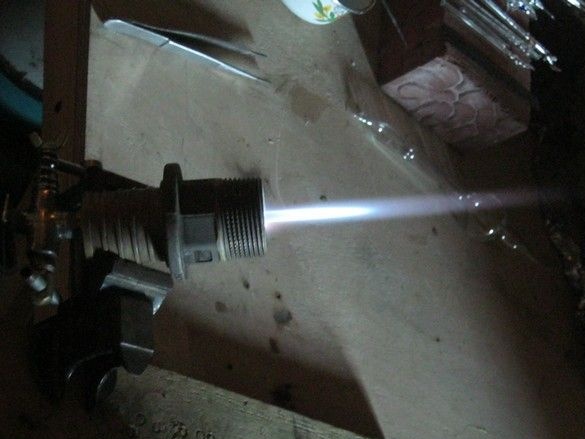

Litteratur.
1. Bondarenko Yu.N. Laboratorieteknologi. Produktion af gasudladning lyskilder
til laboratorieformål og meget mere.