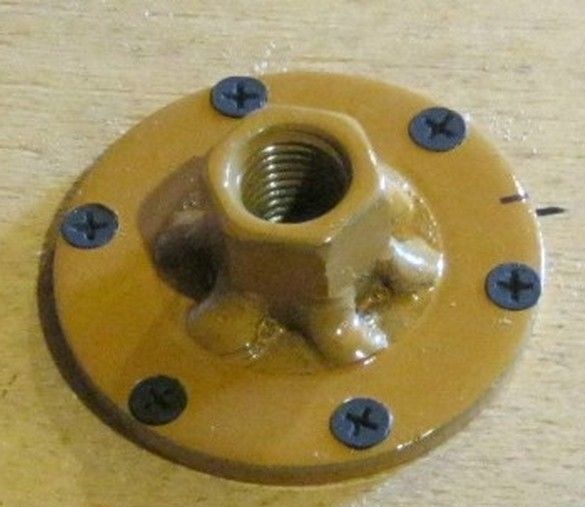
Efter at have konstrueret træ drejebænk, havde det sjovt med simpel drejning i centrene. Efter et stykke tid blev det nødvendigt at behandle mere forskellige arbejdsemner. Jeg var nødt til at bevæge mine hjerner, som fra improviserede midler, uden adgang til en tredjeparts drejebænk (til metal), fremstil det passende udstyr. Et af designerne viste sig at være meget billigt, praktisk og efterspurgt.
Snap-in-fixturen bestod ofte af to dele - en universal lille metalplade og en specialiseret trædel. En metalplade kan også bruges som sædvanligt ved at fastgøre skruer på emnet.
Hvad blev brugt.
Tools.
Selve træbenk, skærer til det, et sæt bænkeværktøjer. Du kan ikke undvære en skæremaskine (grinder), det er bedre at bruge en lille - det er mere praktisk og sikrere. Hovedtelefoner til både skydning og beskyttelsesbriller eller visir. Gå heller ikke ud uden henholdsvis svejsning - en lille inverter og tilbehør. Elektroder 2,5 mm. Ofte brugt hot melt. Det er nødvendigt, at hverken er boring, mere praktisk og mere nøjagtig, det er klart, maskinen.
Materialer.
Faktisk kun det rigtige antal møtrikker og skiver. Det er bedre at male det færdige stykke metal, derefter plus maling. Et lille træ til "smal specialisering", jeg bruger ofte tørt birketræ med lige lag.
So. Spindlen på min drejebænde ender med en M16 tråd, som tillader brugen af standard hardware. I dette tilfælde er dette en "forlængelsesmøtrik." Den skæres i to dele direkte på maskinen, tændes og roterer. Vinkelsliber. Det skal skæres omhyggeligt. Først på en slukket maskine og med en tomgangsslipemaskine i hænderne, prøv forsigtigt på, så det er praktisk, uanset hvor albuerne er, og for ikke at passe ind i noget, der roterer.
Maskinen tændes, og efter vedtagelse af en for-testet positur, tændt med en slibemaskine, slår vi et mærke på markøren midt i den roterende møtrik. Især først omhyggeligt, indtil kanterne er savet, så begynder det at skære mere jævnt, og trykket kan øges lidt.
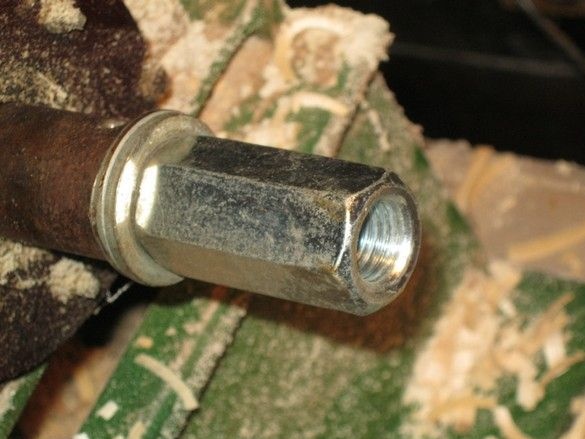
Efter et stykke tid fra vores indsats skæres møtrikens væg igennem, og halvdelen falder væk.Højden på hver halvdel, under hensyntagen til udskæringsbredden, viser sig at være lidt større end dens almindelige søster, der ikke er ”forlængelse”. Længden på tråden på min maskins spindel tillader ikke brug af en almindelig møtrik - den stikker ud under den færdige frontplade og forårsager en masse besvær senere, når du arbejder.
Det næste trin bliver svejsning. Fra standardudvalget af hardware tager jeg en "forstærket skive", i nogle butikker kaldes det en "kropsskive" med en passende diameter. Normalt er dette næsten det største af det tilgængelige sortiment. Du skal kontrollere, om møtrikken falder ned i den. Møtrikken skal stå i midten af hullet i skiven. En afskåret møtrik vil stå bedre - der vil ikke være nogen affasning på den ene side af det, dette skal tages i betragtning, når du prøver på en ny i butikken.
Den afskårne halvdel svejses til skiven. Pænt. Det er meget godt at først stramme dem med en klemme, men som regel viser det sig ret godt. Ribbenene svejses i følgende rækkefølge - hvilken som helst, derefter det modsatte. Arbejdsstykket roterer 90 grader, igen en af de to, derefter det modsatte. Så der er mindre chance for, at møtrikken glider af skiven. I de første eksemplarer forsøgte jeg faktisk at organisere en "rille" med den samme slibemaskine på den roterende halvdel af møtrikken for en sikker pasning i hullet, men vinkelsliberen er ikke det værktøj, der kan udføre dette job godt - ofte på grund af den ikke særlig jævnkant af "rillen" , var møtrikken ikke særlig på linje med skiven.
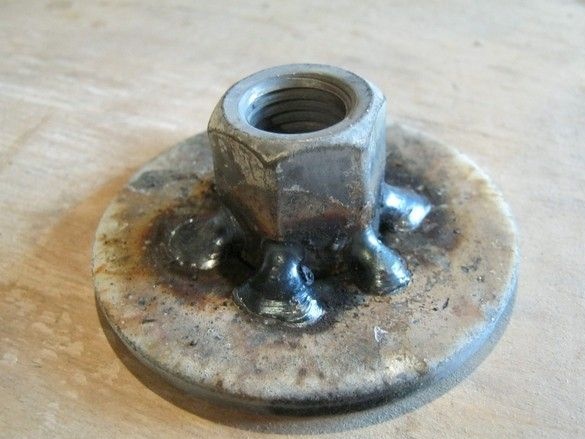
Efter afkøling af emnet, som normalt, omslutter vi glasskorpen af slagge og sætter emnet på maskinens spindel, under rotation vurderer vi udløbet, hvis de er inden for rimelige grænser, korrigerer vi den medfølgende vinkelsliber.

Det er muligt for æstetik og på bagsiden. Her, hvor vi slibes med en blyant på det rigtige sted af det roterende emne, bemærker vi diameteren, langs hvilken hullerne skal bores. For at bruge den fremtidige frontplade med relativt store genstande, kan de bores mere, op til seks, hvis det drejer sig om bagateller - tre, fire.
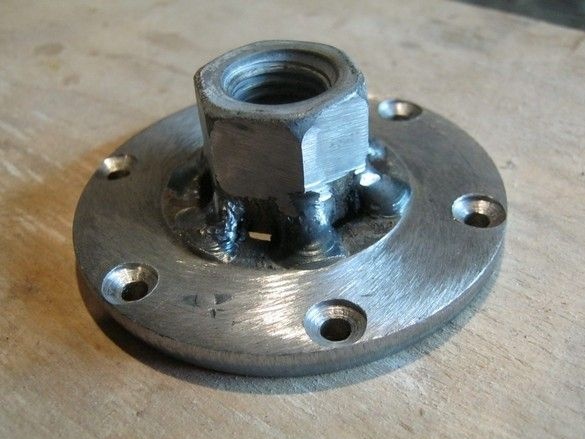
Efter det ville det være rart at male, indtil der er rust - zinklaget er delvist forbrændt, delvist drænet. Nedenunder poppet "oker" fra en sprayboks i to lag, selvom jeg normalt er doven.
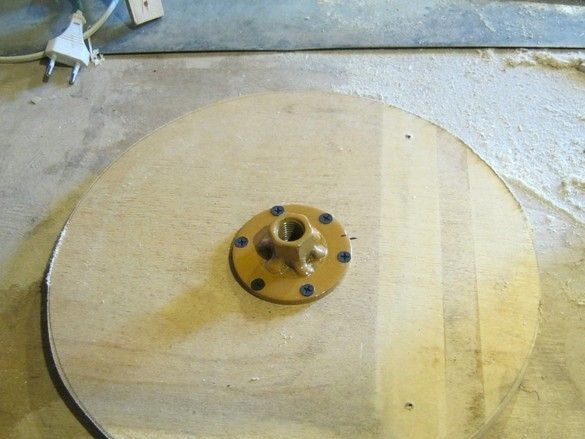
På billedet er den færdige frontplade på slibeskiven lavet af tyk krydsfiner. På en disk undertrykkelse limes PVA-lim, mellemstor, et sandpapir på kludbasis. Gennem et lag aviser, så du kan rive den slikkede sved af.
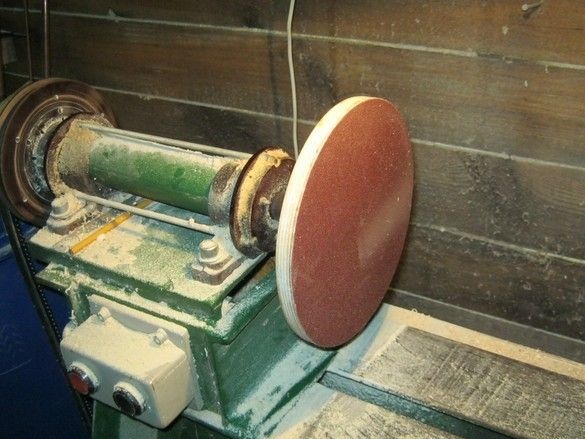
Til slibning af værktøjet skal du montere små træstykker inden limning.
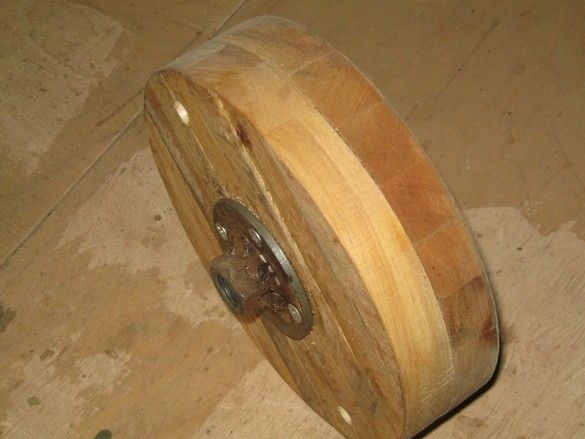
En lignende kontrast, men mindre i diameter og limet fra birkeblokke i to lag med overlapning. Til slibning af drejeværktøj. I slutningen er der det samme sandpapir, et læderbælte limes langs omkredsen til finjustering med GOI-pasta.
Og endelig brugen af vores frontplade til det aktuelle arbejde. Som den sædvanlige er vores lille praktisk at bruge, hvor du har brug for at montere emnet i den ene kant, uden bagerste center. På samme tid er det meget praktisk at lime emnet til mellemblokken. Et stykke bord er ikke fastgjort med lange skruer og drejes til en praktisk diameter, emnet er allerede limet på det. Varmsmeltelim.
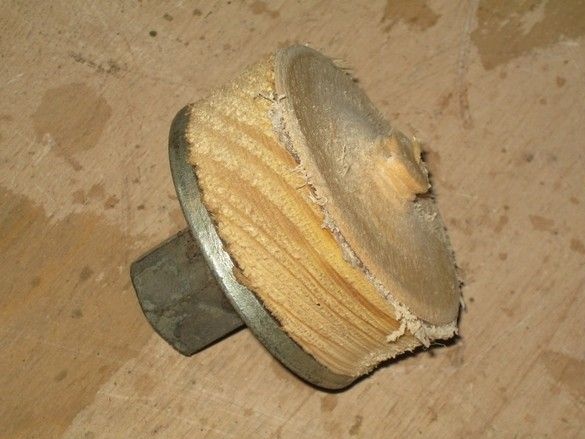
På billedet er der en sådan "patron" med en afgrøde tilbage fra emnet. Før limning af den næste, sættes frontpladen i maskinen og "afskæres" med et skæreværktøj, hvor resterne af den limede en afskæres. Samtidig er det nødvendigt at fange en del af det gamle klæbelag, så det (lim) ikke ophobes for meget.
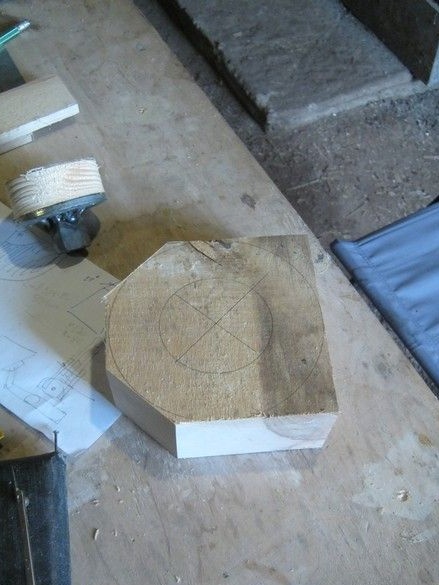
Arbejdsstykket er markeret, mens blandt andet et kompas tegnes en cirkel med diameter lidt større end "blokken" på frontpladen. Dette giver dig mulighed for at orientere den nøjagtigt, når den limes.
Jeg smører begge overflader, der skal limes med varm lim, ikke nødvendigvis fuldstændigt, omkredsen omkring omkredsen er nok, centimeterne rygger væk fra kanten.
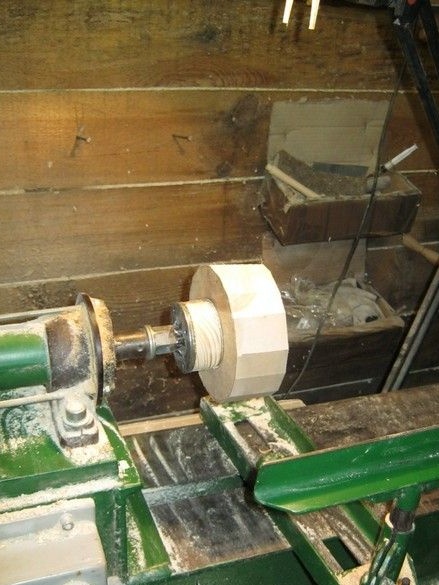
Oprindeligt, før det komplette "narre", er det bedre at trykke på emnets bagerste center, derefter fjernes det, når der ikke er nogen stødbelastning.
Skønheden ved en sådan installation er gennem blokken, i den betydeligt mere økonomiske udgift af emnet materiale, derudover, når du drejer, behøver du ikke konstant at huske, hvor længe skruerne er for ikke at klatre skæren til deres dybde.
Nå, til dessert - der er flere muligheder for en mere specialiseret værktøj baseret på den fremstillede frontplade.
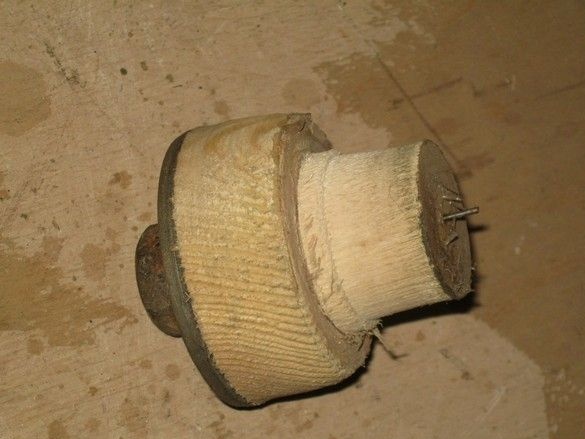
For eksempel blev denne krævet, at noget drejede meget præcist omkring det eksisterende centrum - så let som at beskydde pærer.
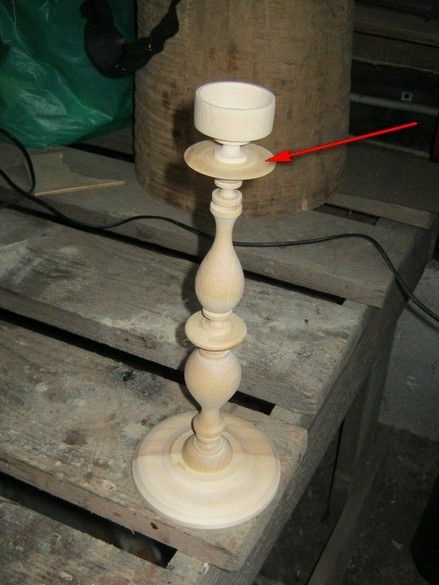
Eller for eksempel - en del af en lysestage lavet af 6mm krydsfiner eller en tynd birkeplade. Til dens spænding og behandling blev der lavet en sådan snap.
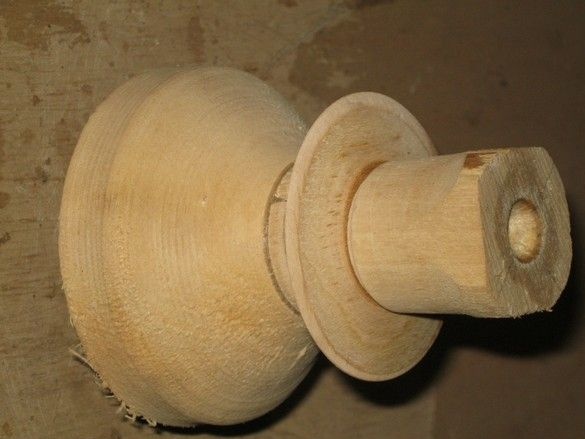
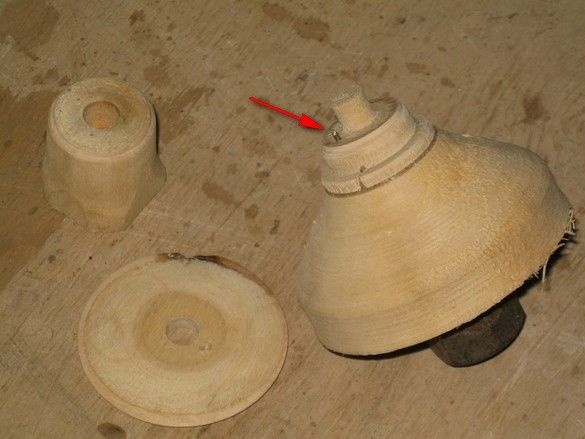
Skarpe nelliker forhindrer, at emnet drejer. Samlet, strammet af bagerste center.
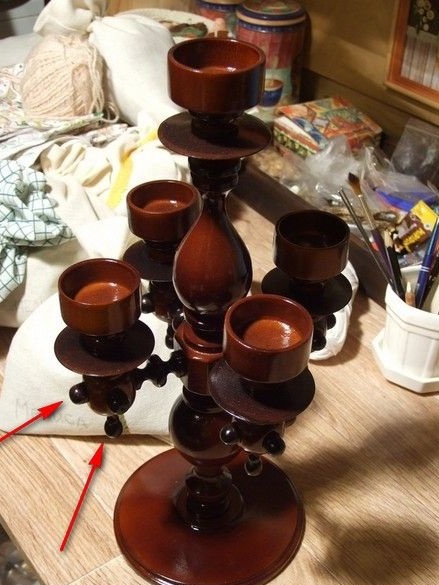
Ved fremstillingen af lysekronen var der behov for et antal små dele, såsom navle, jeg var nødt til at lave en simpel trækuglebånd.
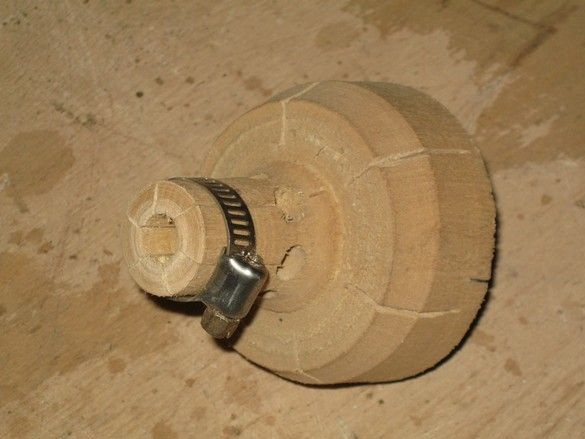
På trods af de noget begrænsede kapaciteter har det også en række fordele, nemlig fremstilling af let, lave omkostninger. Når man behandler miniature-dele, i nærheden af de mest ”kæber”, skal man ikke være for bange for at koble “patronen” med et værktøj, som i tilfælde af at bruge en metalfabrikanalog nogle gange har fatale følger. Ja, sikkerhed er igen et minimum af fremspringende dele, de kan reduceres endnu mere, hvis du udskifter en metalormklemme med udglødet stål- eller kobbertråd eller endda laver en lille konisk udvendig side af kæberne og fylder ringen til klemme. Metal eller træ.
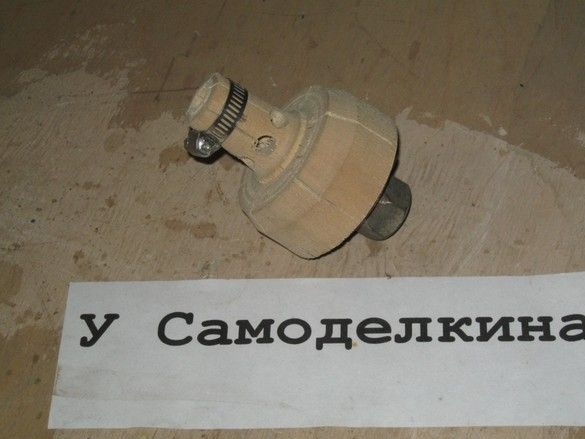
Ved fremstilling af en spændebånd drejes først cylinderen, et centralt hul (en boremaskine) bores, huller markeres og bores på siden. Derefter, i drejebænken, bearbejdes den fremtidige klemme - ikke-tykke kæber dannes. Til sidst lavede han udskæringer af båndbladene.